WAREHOUSE MATERIAL SPECIALIST JOB DESCRIPTION
Find detail information about warehouse material specialist job description, duty and skills required for warehouse material specialist position.
What does a material specialist do?
Materials scientists and engineers work on many different types of materials in order to create the products they use every day. They study the properties of materials and make sure they are used in the right way for a particular task. Materials scientists and engineers can be involved in research or development of anything from paint to lasers. They are responsible for the safety and effectiveness of products, as well as making sure that materials are used properly.
What is the job description for a warehouse specialist?
The warehouse specialist oversees daily operations in a warehouse. They are responsible for coordinating shipping schedules, tracking inventory, or running team meetings. This position is a management position, so additional duties include supervising the warehouse workers and shipping and receiving clerks. The warehouse specialist is a essential part of any business, and their skills will help to keep your business running smoothly.
What are the duties of a logistics specialist?
Most logistic specialists work with a variety of different products and services to help make life easier for customers. They may be involved in preparing goods for shipment, tracking the progress of shipments, or even providing customer service. In addition to their work with logistics, these specialists may also be familiar with accounting and management software.
What is a material administrator?
It is an importantrole in a company to have a materials manager. They are responsible for overseeing the planning and coordination of a company's inventory and purchasing departments. They are also responsible for researching best prices, monitoring inventory levels, distributing supplies, and negotiating contracts.
What is a raw material specialist?
A raw material specialist prepares the specifications for raw materials and primary packaging. They also inspect incoming raw materials to ensure it meets specifications and evaluate release / reject disposition. The specialist is important in ensuring that the quality of the raw materials used in a product is met and that they are able to be released or rejected accordingly.
What is a materials manager job description?
The materials manager will be responsible for all aspects of the company's material management including procurement, storage, distribution, and control. They will work to ensure that materials are used efficiently and in the best possible way to meet company goals.
What is a warehouse logistics specialist?
The warehouse logistics specialist is responsible for various tasks such as managing the stock room, which contains the receipt and storage of properties, reserving space allocations for properties and items, and managing specialized storage requirements. They are also responsible for creating a plan that will optimize the use of space and improve efficiency. This position is an important one in any organization, as they must make sure that all objects are stored in a way that allows them to be accessed and used quickly.
What is a warehouse generalist?
The Warehouse Generalist will be responsible for ensuring that all warehouse functions involve, retrieving, moving, and stacking merchandise. They will use material handling equipment excluding forklifts to do this. The Warehouse Generalist must be able to write creative English paragraphs that are descriptive of their job.
What is an Amazon Logistics Specialist?
When the data center is under renovation, the Logistics Specialist will be ensuring that the proper stock levels are maintained in all locations to support build and repair activities. By keeping track of in-bound shipments and demand, they can ensure that the data center is able to operate at its peak potential.
How do I write a logistics resume?
The logistics resume objective is to show an employer that you have the skills and experience to work in a supply chain management role. The resume summary should list your past duties, with examples of achievements that demonstrate your skills in this particular field. The resumes will also show that you are a people person, able to get along with others and take on multiple tasks at once.
What are the skills required in a material manager?
Keith is a skilled supply chain and inventory management consultant with over 10 years of experience. Keith has expertise in forecasting and budgeting as well as in communicating with others in the supply chain. He is also excellent at working with other teams and managing his time.
What degree do you need to be a Materials Manager?
A materials manager is responsible for ensuring that all materials used in a hospital are safe and properly managed. This includes ensuring that medical supplies are protected from contamination, tracking inventory levels, and managing the flow of materials to and from patients. A materials manager's education must include at least a four-year degree from a regionally accredited college or university.
Who is responsible for material management?
A purchasing manager is responsible for all aspects of the purchase of raw materials and finished goods in a business. They must compare prices and determine the quality of products a company will use to build products or sell to customers. A buyer is responsible for verifying the quality of products before making a purchase.
What material management means?
Construction management is the process of planning and controlling all materials and equipment so they are requested in advance, obtained at a reasonable cost and are available when needed. This definition includes not only materials that go directly into construction, but also products that will be used in the construction process, such as tools and machines. By taking these precautions, construction managers can avoid costly shortages and ensure that all required resources are always available.
What is the difference between material management and supply chain management?
A supply chain management system (SCM) is a comprehensive approach to organizational planning, organization and control of a network of businesses that provide product and service packages required by end customers. The system relies on a tangled web of materials and components to ensure the smooth flow of goods throughout the supply chain. A SCM framework includes the following: 1. The organization of the supply chain. This includes the creation of an inventory, transportation, material delivery, and customer information systems (CIS) to manage the flow of materials and components. 2. The creation of transportation plans that include accurate information on how long each step in the supply chain will take and how much money will be spent on each trip. 3. The management of material delivery systems to ensure that all necessary parts are ordered in advance and delivered when needed. 4. The management of customer relationships through CIS to ensure that every order is filled quickly and correctly with minimum disruption to service
What is importance for material manager?
In an organization, material management is important in order to improve efficiency. This saves the organization time and money. Material managers must adopt efficient systems in order to ensure this. Without efficient systems, material management objectives are ineffective.
What is a supply chain specialist?
A supply chain analyst, or supply chain specialist, is responsible for ensuring the company's supply meets the customers' demand. They are responsible for overseeing the company's supply chains, ensuring timely delivery and keeping the company on budget. A good supply chain analyst will be able to identify and understand the company's needs and make necessary changes to ensure that they are met.
Is logistics a good job?
The English writing market is ever-changing and expected to grow at an annual rate of 10% in the coming years. With so many talented writers out there, it's no surprise that businesses are scrambling to find the right talent to fill their needs. One of the best options for businesses looking to hire talented writers is through online writing communities. These platforms allow businesses to connect withwriters who share their same interests and can provide valuable feedback. Additionally, many newspapers and magazines are now hiring freelance writers. This means that businesses can search for writers who have some experience writing in a specific area and not just those with a lot of creative output.
Can you get into logistics without a degree?
A business analysis degree or a business administration degree can help you become a logistics professional. A business analysis degree provides you with the skills and knowledge needed to understand the economics of businesses and the delivery of supply-chain solutions. In addition, a business administration degree can help you build your resume by providing you with the skills and knowledge needed to manage a company's finances and operations.
What does a logistics job look like?
A typical job duties include developing relationships with suppliers, ensuring all materials are transported on time, understanding customer needs and finding ways to minimize the cost of moving goods and materials. With years of experience, the supplier relations specialist understands the nuances of moving goods and materials. They are able to identify potential problems before they happen and work to solve them as quickly as possible.
How much do Amazon Route owners make?
At Amazon, truck drivers are able to earn a salary of up to $300,000 a year, or $7,500 per route per year. This type of work can be rewarding as it provides stability and a good income. Drivers at Amazon can work long hours and be available on short notice.
What knowledge is needed for logistics?
In the field of logistics, there are many skills that are needed to succeed. Some of these skills include reading and analyzing data, and making interpretations that can be helpful to the company. A career in logistics can be a very rewarding one, as you will be able to use your skills to help make a positive impact on your company.
What are hard skills in logistics?
Logistics skills are critical for businesses of all sizes. From organizing and managing stock to shipping products to customers, these skills are essential for running a smoothly efficient supply chain. Some popular logistics skills include logistic management, supply chain management, operations management, warehouse operations, and warehouse management systems. In order to run a smoothly efficient supply chain, businesses must have these skills in order to effectively manage their stocks and shipping products.
What is logistic experience?
A typical logistics activity includes procurement of materials, storage, transportation and distribution of the finished product. This can be a hidden area of cost savings for companies that do not currently have a logistics department. You may be hired directly onto a company's payroll or work as an outside consultant.
What is material management experience?
Inventory management is a critical function in any business. Managers must keep track of the current stock of items and make sure that it's enough to meet company needs. They also need to maintain accurate records to ensure that the correct inventory is being kept.
Who reports to the Materials Manager?
Materials Manager is responsible for planning and forecasting customer orders to meet shipments. They work with product line coordinators on the planning and forecasting of customer orders to meet shipments. Materials Manager typically reports to a Head of a Unit/Department. The responsibilities of a Materials Manager include: 1) Work with product line coordinators on the planning and forecasting of customer orders so that they can be met as quickly as possible 2) Work with suppliers to get the best materials price quotes for their products 3) Work with customers to ensure that they have what they need when they need it 4) Keep track of inventories and suggest ways to reduce them
Which is part of material management?
material management is a process that includes planning and controlling material flows. It includes planning andprocuring materials, supplier evaluation and selection, purchasing, expenditure, shipping, receipt processes for materials (including quality control), warehousing and inventory, and materials distribution. By managed through these processes, companies can ensure that they receive the best possible quality for their products.
How do I become a material controller?
As a material controller, you will be responsible for managing the flow of materials through your company. This will include ensuring that all materials are properly stored, transported and delivered to the right locations. You must be familiar with safety regulations in order to ensure that everyone is safe while working with materials.
What is material executive?
The Material Management Executive is responsible for all aspects of the purchase, storage, and distribution of raw materials, supplies, and equipment needed for the production process. They ensure that inventory needs are met throughout the production process while maximizing the efficiency of warehousing and distribution operations. This individual is also responsible for ensuring that employees are well-prepared for work with respect to material handling and transportation.
What is SAP MM module?
SAP Materials management is a module of the SAP ERP software package that is used for procurement handling and inventory management. It covers all tasks within the supply chain, including consumption-based planning, planning, vendor evaluation and invoice verification. SAP Materials management offers a variety of features that can help you manage your supply chain better, including: -Consumption-based planning: This feature enables you to plan for future demand by figuring out how much resources you will need to purchase based on the current market conditions. -Planning: This tool helps you identify which resources will be needed in the future and then assign those resources to specific suppliers. -Vendor evaluation: This tool helps you determine which suppliers are best suited to meet your needs and then issue invoices accordingly. -Inventory management: This module helps you keep track of your current inventory levels and determine what needs to be replaced or updated in order to keep your business running smoothly.
What is material management called?
Materials management is a core function of supply chain management that involves the planning and execution of supply chains to meet the material requirements of a company or organisation. By managing shipments effectively and efficiently, companies can save money and ensure that their products are of the best quality.
What are the five major areas of materials management?
Strong leadership and a well-developed materials management system can help to ensure a successful launch. Leaders understand the importance of keeping materials safe and organized, and know how to create systems that work well. By creating a strong materials management system, organizations can ensure their launches are successful and efficient.
What are the problems of materials management?
The challenges of material management are often faced by businesses as they face a variety of changes in their projects. One such challenge is exceeding the initial planned budget. This can be done by either purchasing too much material or overbudgeting on the original plan. Additionally, the handling of material can be difficult when there are large changes in plans or when it is necessary to move objects around on the job site.
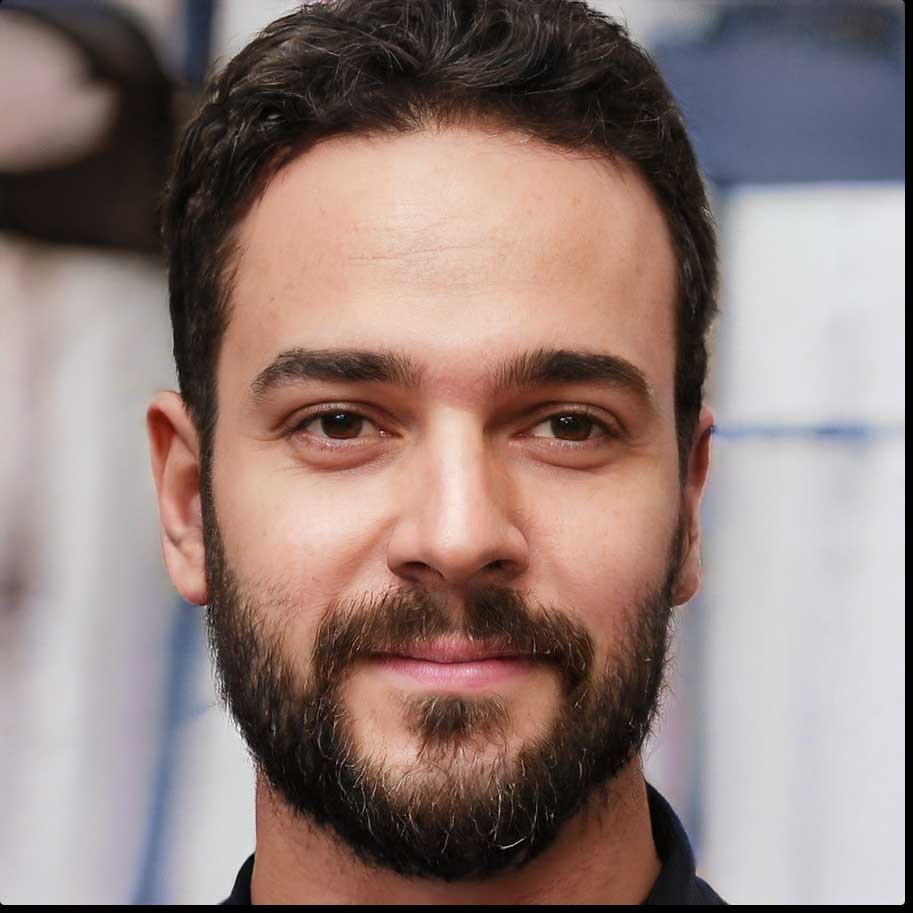