QUALITY INSPECTOR JOB DESCRIPTION
Find detail information about quality inspector job description, duty and skills required for quality inspector position.
What is the job role of quality inspector?
A quality inspector is a professional who is responsible for ensuring that manufactured products meet all requirements. They use tools and company guidelines to make sure products have been perfectly crafted and are ready for the consumer. They are also responsible for inspecting products during the manufacturing process to ensure that it meets all requirements.
Who is a quality inspector?
A quality control inspector is responsible for monitoring the quality of incoming and outgoing products for manufacturing companies. QC inspectors, also called quality controllers (QC), are members of a control audit team that examine manufacturing processes and operational techniques. They are responsible for ensuring that the products they produce are of high quality and meet the needs of their customers.
What are the qualifications of a good inspector?
The Quality Control Inspector is responsible for ensuring the quality of products and services. They are responsible for checking products to ensure they meet all safety and quality requirements. The inspector also monitors the performance of services and ensures that they are meeting customer expectations.
What makes a good quality inspector?
The Control Inspector is responsible for maintaining the quality of products and services by ensuring that the products and services meet specific specifications. The Control Inspector has excellent problem-solving and analytical skills, as well as basic computer and math skills to calibrate and measure specifications. They are also able to use measuring devices like gauges, meters, calipers and computers. The Control Inspector's ability to write creative English paragraphs helps them to maintain a high level of quality in their work.
Is a quality inspector an engineer?
QC engineers are responsible for ensuring the quality of products and services produced by their company. They oversee the manufacturing of products and they are involved in every stage of making a product--from development and manufacturing to packaging. QC engineers play an important role in ensuring that products meet all the required standards, from design to quality control. This involves ensuring that products are made to specification, that there are no defects, and that they aresafe to use.
What is QA QC inspector?
A QC inspector watches over products to make sure they meet the company's specifications. They test products to make sure they are working correctly and that they are not defective.
What is the salary of quality control officer?
A Control Officer salary in India can range from Rs 1.7 lakh to Rs 5.2 lakh with an average annual salary of Rs 3.1 lakh. These officers are responsible for monitoring and controlling various aspects of a company, ensuring compliance with regulations, and maintaining communication within the organization.
How can I become a QA officer?
QA officers work in the food industry to ensure that products are of high quality and meet the needs of consumers. They are responsible for ensuring that products are safe and meet all safety regulations. QA officers can also help to improve product performance by verifying that ingredients and manufacturing processes are consistent with each other.
What are the 4 types of quality control?
Four different methods of quality control are commonly used in the manufacturing process. These include an x-bar chart, Six Sigma, 100% inspection mode, and the Taguchi Method. The Taguchi Method is a Japanese method that uses a qualitative judgment to measure the quality of products. This method is often used in the manufacturing of electronic goods because it can provide a more accurate estimate of how well products are performing.
Is QA QC a good career?
The growth of the mechanical engineering profession is significant, and there are many great options for those with a science background or experience in QA and QC. As a mechanical engineer or someone with a science background, you may have a better chance of finding a job in this industry than any other. With the increasing popularity of NDT, this technology is sure to keep growing.
What is QA QC experience?
Quality assurance and quality control are two important steps in ensuring the quality of products. Quality assurance ensures that the product meets consumer expectations and quality control ensures that products and services meet consumer expectations.
Is quality engineer a good career?
In the industrial engineering field, quality engineers are responsible for ensuring that products and systems meet specific standards. This involves creating or modifying products to ensure they are safe and effective, as well as designing and building systems. The field is projected to grow by 10% between 2016 and 2026, making it an excellent choice for those who want to work in a high-growth industry.
What are quality control skills?
World-class quality assurance teams work together to ensure that products and services meet customer expectations. By understanding the work that others in your department do, you can help them achieve their quality standards. This understanding helps you collaborate to achieve your business' goals.
Which is better QA or QC?
QA creates and ensures the processes are being followed to ensure quality. QC measurement results can be utilized to correct/modify QA processes which can be successfully implemented in new projects as well.
What degree do you need to work in quality control?
Entry-level quality control inspectors should have a high school diploma or equivalent. Their job opportunities and earning potential are increased by having a bachelor's or associate degree in quality assurance. A high school diploma or equivalent gives an inspector the skills and knowledge necessary to carry out quality control inspections.
What are the courses for quality control?
In today's competitive business world, companies must manage and maintain their quality in order to remain competitive. This can be achieved through various means such as good communication, effective monitoring and control systems, and effective communication with customers. The ISO 9001:2015 quality management system (QMS) is a comprehensive system designed to ensure that products and services meet specific requirements. It is important for businesses to understand the system and how it can be used in order to improve the quality of their products. A key part ofISO 9001:2015 is the Quality Management Courses (QMCTs). These courses provide managers with knowledge and skills needed to carry out effective QMS activity. The cost of these courses is often high, but they are worth taking if businesses want to improve their quality standards. Finally, a certified Quality Engineer (CE) can help businesses realize improvements in their quality standards. These individuals have years of experience in working with various aspects of quality management, so they are able to bring about significant improvements in the overall process.
What is QA in pharma?
QA covers all aspects that could have an impact on the quality of prescribed pharmaceutical products. It includes ensuring that products are safe to use and that they meet the requirements of scientific standards. This can include checking for potential side effects and ensuring that the product is effective.
What are 5 different quality control methods?
There are seven primary quality control tools which include: checklists, fishbone diagram, control chart, stratification, pareto chart, histogram, and scatter diagram. Each tool can help you to ensure that your product meets specific quality standards. By using these tools, you can improve the quality of your products and increase their sales potential.
What are the 4 steps of quality control?
It is important to have a quality management process when starting a business. By having a process in place, you can ensure that your business is meeting the standards set by others. This will help you to maintain customer trust and ensure that your products or services are of the best quality possible.
What are the 3 types of quality?
Customer satisfaction is a key factor in any industry. In the customer service industry, basic quality is important because it allows customers to feel comfortable and satisfied with their purchase. Performance quality is important because customers want to be able to expect the best from their products. Excitement quality is important because it provides customers with a sense of anticipation and excitement about their product or service.
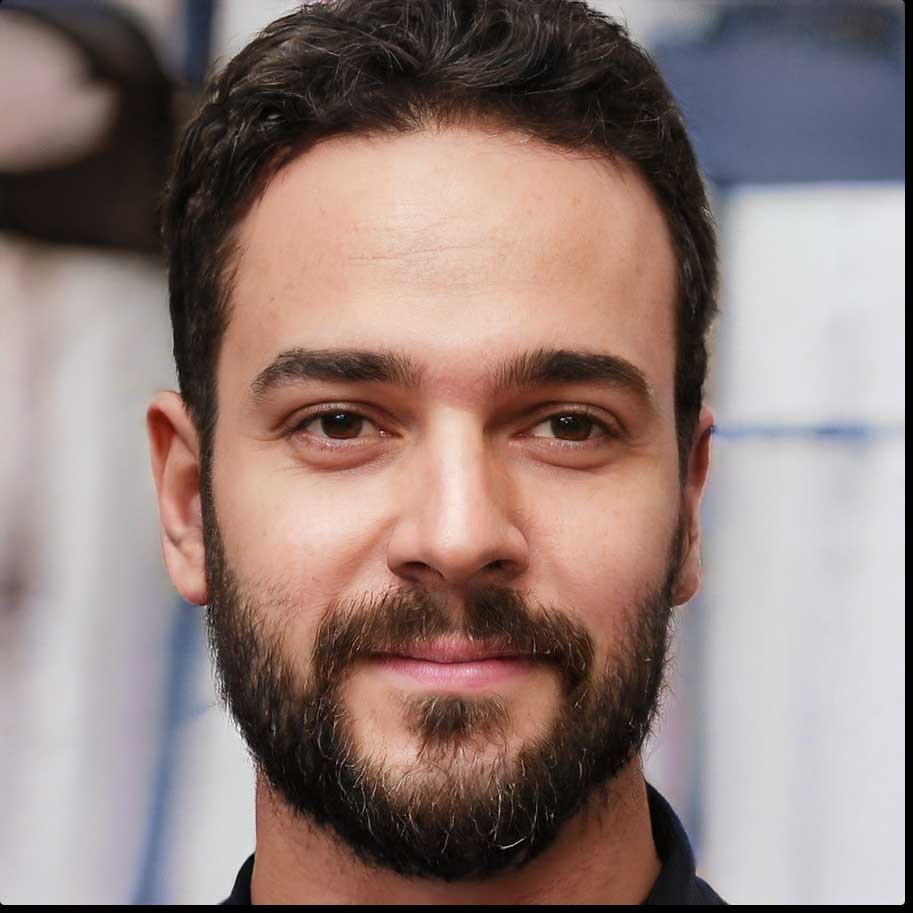