QUALITY CONTROL OFFICER JOB DESCRIPTION
Find detail information about quality control officer job description, duty and skills required for quality control officer position.
What does a quality control officer do?
The testing and assessment of products is an important part of any company's quality control process. The role of the product control officer is to identify product defects or potential issues and determine what to do to resolve them. They also need to support process improvements throughout the testing and quality assurance processes.
What are 4 types of quality control?
When it comes to quality control, it's important to adhere to specific processes and guidelines in order to ensure the quality of your product. Acceptance sampling is a valuable method of ensuring that the product is meeting customer expectations; control charts help you track and measure the progress of your product in order to make necessary changes or adjustments.
How can I become a QC officer?
The Quality Control Personnel position is a vital role in many companies. They are responsible for ensuring the quality of products and services before they are released to the public. The person must have a degree in a related field, and be able to work with other individuals and groups.
What are 3 examples of quality control?
Quality assurance activities include inspection, deliverable peer reviews and the software testing process. Inspection is a critical step in the quality assurance process to ensure that products meet the specific requirements of the target audience. By looking for potential issues early, developers can correct them before they cause problems down the road. deliveredPeerReviews are another important quality control tool. They allow users to rate and comment on products to help identify any problems early on. Finally, software testing is an essential part of quality assurance and helps determine whether a product is safe and effective.
What are 3 types of quality?
Customer satisfaction is important in any industry. Basic quality must be upheld in order to maintain customer loyalty, while performance quality must be top-notch so customers are happy with their purchase. Excitement quality must be high enough to keep customers coming back, and finally, the product must meet or exceed customer expectations in all areas.
What are the 3 main objectives of quality control?
A quality control program is necessary for any manufacturer with a product. A robust and functional program helps ensure that products are of excellent quality and are able to meet customer expectations. This will help to gain production efficiencies and generate loyalty from customers.
What are the different types of quality control?
There are many different types of quality control, but four of the most common ones are an x-bar chart, Six Sigma, 100% inspection mode, and the Taguchi Method. An x-bar chart is a tool that can be used to measure the quality of products. This method is often used in manufacturing because it is easy to track how well products are performing. Six Sigma is a method used to improve the quality of products. This method involves setting specific goals and then constantly measuring how well those goals are being met. 100% inspection mode means that all product features must be check before they are made available to customers. This method is often used in food production because it allows for quick and accurate inspections.
What are two types of quality control systems?
Quality control is the process of ensuring that a product or service meets customer requirements. Quality assurance is the process of confirming that the product or service meets customer requirements.
What is quality control checklist?
A quality control checklist is a guide to ensuring the quality of your products. It includes important safety and quality requirements for your products. This document is also sometimes called an inspection criteria sheet or inspection checklist.
What is Six Sigma methodology of quality control?
The Six Sigma process helps businesses improve quality control in their manufacturing or business processes. By discovering and eliminating defects, this methodology decreases the risk of variation throughout the organization. This ultimately leads to increased product or service quality.
Is quality management a good career?
Quality management is a field that ensures that only acceptable, functional, quality products are distributed to businesses and consumers. This field requires a keen eye for detail and top-quality goods. A career in quality management can provide you with the skills and experience you need to help your business achieve its goals.
What are quality control skills?
A quality control standard is a set of guidelines that a company or organization must follow in order to ensure the quality of their products. The standard is typically written by a committee comprised of experts in the field. It is important to remember that these standards are not always 100% accurate, and companies should always check to see if their product meets any specific standard before selling it. Some common quality control standards include checking for defects in products when they are manufactured, checking for conformity with industry standards when products are sold, and verifying that samples meet customer demand. In order to meet these standards, companies usually require employees to be familiar with certain mathematics and statistics. As well, companies often require sample sizes to be small enough so that there is no chance of causing too much variation across different customers.
What is quality control in simple words?
QC is a procedure or set of procedures intended to ensure that a manufactured product or performed service adheres to a defined set of quality criteria or meets the requirements of the client or customer. QC is similar to, but not identical with, quality assurance (QA). QC can help ensure that products and services meet customer expectations and are of high quality. QC can also help ensure that products are consistent across different batches and regions.
What are the 4 steps of quality control?
Most quality management processes include activities such as planning, assurance, control and improvement. Planning ensures that all aspects of the quality system are considered before making any decisions. Assurance ensures that the quality system is functioning as intended and that no errors are made. Control measures ensure that the quality system is kept running smoothly and on schedule. Improvement efforts focus on increasing the efficiency and accuracy of the quality process so that it can be used effectively in the future.
What are the 5 types of quality control?
Fishbone diagram is a control chart that helps you to analyze your product's performance. The diagram shows the relative strengths and weaknesses of your product. You can use this information to improve your manufacturing process.
What is quality control PDF?
QC is a process of ensuring the conformity of the results (outcome, products) to established criteria or standards. It may include activities such as testing and measuring equipment, product specification, and quality assurance procedures.
What is quality control and examples?
Quality control is a process that ensures the accuracy of products. In a manufacturing plant, this includes checking each item to make sure it is correctly put together. This helps to ensure that the product is of good quality and meets customer expectations.
Where is quality control used?
In food and drug manufacturing, quality control is important to ensure that products are safe for the general public to use. In this industry, quality control methods often include employees who pay close attention to their work. This ensures that products are of good quality and do not cause any harm to customers.
What is quality control a level?
Quality control is a process that ensures that products meet the required quality standards. This process checks the quality of completed products for faults. By doing this, it can help to ensure that the products are of good quality and are worth buying.
Why is quality control needed?
A business that control its quality and produces products that meet or exceed customers' expectations is a successful one. high levels of productivity and waste reduction are also essential to this type of business.
What is quality control Example?
Quality control is a important process in manufacturing. The department that is responsible for inspecting products to make sure they are properly put together uses a variety of methods to ensure that their product meets the standards set. Some of these methods include checking for accuracy, quality, and conformity.
What is the difference between QA and QC?
QA is a process that is used to ensure the quality of a product. It focus on the procedures and processes that are used to improve the quality of the product. QC is more focused on finding defects that remain after development.
What are the five 5 different quality control methods?
The seven primary quality control tools are checklists, fishbone diagram, control chart, stratification, pareto chart, and histogram. Each of these tools can help you to identify any problems with your product and ensure that it meets the necessary standards.
How do I write a QC report?
A quality assurance report (QAR) is a document that is used to ensure the quality of products. A QAR may be used to measure the quality of products, such as in the case of manufacturing, product testing, and end-user inspections. In order to create a QAR, an auditing or testing methodology must be established. This will allow you to determine how well each step in the manufacturing process meets the requirements for quality. The findings of your QAR will then provide you with insights into areas where improvement may be made. Additionally, appendices can be created that present data related to specific areas of concern in order to help manufacturers address these issues more effectively. Finally, it is important to conduct regular Quality Assurance (QA) audits in order to remain up-to-date on changes and improvements that may occur within your industry.
What is the first step in quality control?
The first step in quality control is to determine criteria and standards. Measuring performance or making corrections is impossible if standards have not been clearly established. Standards help to ensure that the product meets the desired standard, and that any errors are caught early.
What is another word for quality control?
Quality assurance is a process that ensures the quality of products or services. It can be used to refer to different aspects of the quality-control system, such as checking products for compliance with safety and quality regulations, inspecting manufacturing processes, or verifying product authenticity. Quality assurance can be achieved through a variety of methods, including physical and technical inspections, interviews with key stakeholders, and laboratory testing. Sometimes, it is necessary to combine these methods in order to ensure a coordinated and effective process. There are a number of different terms used to describe quality assurance: quality control, vetting, review, q&a, cross-check, survey, traceability, process control, ISO9000 and OH&S. However, the most common term used in practice is quality assurance.
Why it is called Six Sigma?
Six Sigma is a system of manufacturing that is used to improve the quality of products. The goal of Six Sigma is to reduce the number of defects by 90%. When a company begins using Six Sigma, they typically achieve this goal by reducing the number of process events by 60%. This decreases the chance that a defect will occur by 3.4%.
Which company use Six Sigma?
Most companies that claim to have implemented Six Sigma in some form or another are large, multinational corporations. Three of the largest companies in the world, 3M, Amazon, and Atos, are all known for their successful implementations of Six Sigma. These companies have made a name for themselves by implementing quality control measures that aim to improve the productivity of their employees.
What are 6 sigma tools?
Six Sigma tools are used to support process improvement efforts. The Six Sigma expert uses qualitative and quantitative techniques to drive process improvement. By using these tools, they can help improve the quality of their work.
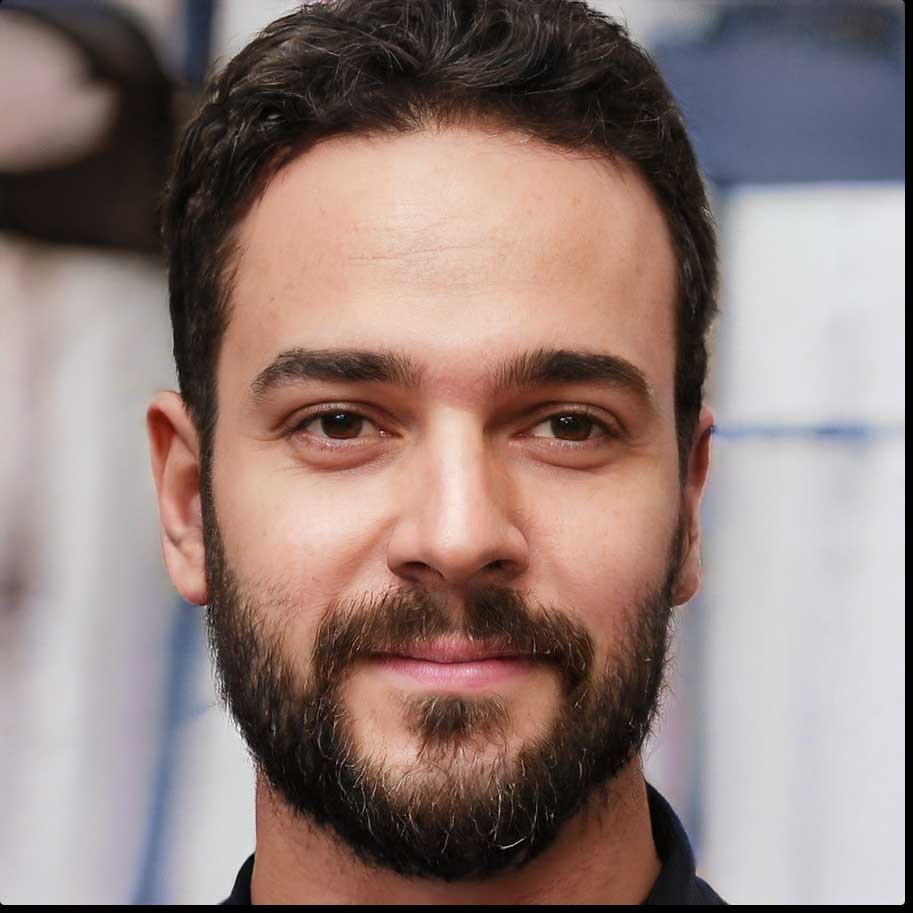