QUALITY CONTROL LEAD JOB DESCRIPTION
Find detail information about quality control lead job description, duty and skills required for quality control lead position.
What does a quality control lead do?
Usually, when a contractor is contracted to do work on a project, they will be working with an engineer who will help them with the design, and then the construction will take place. This is usually done through a team of engineers who will be working together. The QA/QC Lead is responsible for ensuring that the quality of the work meets or exceeds the project's contractual requirements. They will typically be working with other engineers in order to make sure that all aspects of the project are put together in an accurate and efficient manner.
What is quality lead position?
A QA team lead is responsible for the quality assurance team within a software development organization or department. They are in charge of developing, implementing and managing test plans. Their main job is to ensure that quality standards are met. A QA team lead can help to improve the quality of a product and make it more efficient.
What do you do in a quality control job?
The inspectors at production facilities and retail locations are responsible for ensuring that products being produced or sold meet the expectations of consumers. They examine materials to make sure they meet quality expectations then assess the final product after production. This ensures that the product is of good quality and meets consumer expectations.
What is the salary of quality control officer?
Requirements of a security control officer in India are rigorous and vary depending on the company. The average salary for such a position in India ranges from ? 1.7 Lakhs to ? 5.2 Lakhs with an annual salary of ? 3.1 Lakhs. The demand for security control officers in India is high due to the increasing number of attacks and incidents that take place in the country. Companies must be careful with their investment as a security control officer will play a critical role in maintaining order and protecting resources.
What is the difference between QA Lead and QA manager?
A Lead is a working leader who assists and trains those who are under him/her, but is not responsible for their actions. Whereas a Manager is responsible for those who report to him/her. The Manager assigns, monitors, and evaluates the reportees.
Is quality control a good career?
In quality control and assurance, people work to ensure that products are of the highest quality. They must have a keen eye for detail, strong communication, planning and problem-solving skills. This job is important in industries such as aerospace and automobiles, where quality is often key to success.
What skills does a quality control manager need?
As a quality control manager, you need to be excellent at communication and listening skills. You should also have strong observational, analytical, and problem-solving skills. These skills will help you understand regulatory compliance and be able to understand scientific and technical data. Because of this, you will be able to provide quality control systems with the necessary information to ensure that products are meeting the required standards.
How do you become a quality control manager?
As a quality control personnel, you will be responsible for ensuring that products meet the company's standards. This involves inspecting products to make sure they are of the correct size and shape, as well as checking for any defects. You will also be responsible for maintaining records of product testing and results, as well as tracking customer satisfaction levels.
What are the 4 types of quality control?
Many methods of quality control are available, including an x-bar chart, Six Sigma, 100% inspection mode, and the Taguchi Method. The Taguchi Method is a specific way of ensuring product quality by counting defects.
What are quality control skills?
At the company, they take pride in the quality control standards and legal standards. The knowledge of data analysis, mathematics, and statistical techniques enables us to ensure that the products are of the highest quality. The previous experience in manufacturing and production processes allows us to quickly and efficiently produce the product they need. The communication, problem-solving, time-management, and leadership skills make us a great team player.
What are some examples of quality control?
QC is an important process in the development of products. In it, products are inspected to ensure that they are of the required quality. Inspection activities include review of deliverables, peer reviews and software testing.
Which one is better QA or QC?
Quality assurance is the process of ensuring that the products or services provided are of high quality. QC is a measure of how well a product or service meets expectations and can be used to correct any deficiencies in the process. QC can help to ensure that products or services are delivered to customers in an optimal condition.
How can QA lead be improved?
One of the most important aspects of a successful software development process is ensuring that all the pieces of the application are functioning correctly. However, often times, it can be difficult to do this because there may be multiple parts of the software that are not always integrated correctly. This can lead to significant errors and potential setbacks in the development process. To make sure that all concerned parties are on the same page and that everyone is able to contribute their best effort, it is recommended that someone owns QA. This will allow them to have a say in how everything is done and will also help ensure that all parts of the application are working properly as a whole. Additionally, integrating your team more will make it easier for everyone to communicate and work together as a team. By doing so, errors will be less likely to occur and ultimately, the development process will move faster and be more error-free.
Is quality control a stressful job?
It can be a bit challenging, but the work of a QA specialist is actually quite relaxing. They ensure that the quality of the product is up to par, and that the tests are accurate. This can be a bit exhausting, but it can lead to some professional growth.
What is next after quality control?
A Quality Control can determine their career goals through the career progression. For example, they could start out with a role such as Quality Assurance, progress to a title such as Quality Assurance Lead and then eventually end up with the title Quality Assurance Manager. A quality control's job is to ensure that products and processes are of high quality. By understanding their career path, they can plan for their future and achieve their career goals.
What qualifications does a quality manager require?
A quality manager is responsible for ensuring the quality of products and services. They are responsible for ensuring that products and services are meeting customer requirements and expectations. A quality manager must have a keen eye for detail, as well as a results-driven approach. They must be able to communicate effectively with their team and clients. A quality manager is also proficient in Microsoft Office, which can be helpful if they need to create reports or graphs.
What are the 2 types of quality control?
A product must be inspected for quality before it is sold. This includes assessments of its physical properties, such as the materiality of features and the construction of the product. inspection can also include tests to ensure that the product is functioning correctly.
What are the 3 main objectives of quality control?
One of the benefits of using quality control measures is that they help to ensure that products are of high quality and meet customer expectations. Quality control can help to improve production efficiency, as well as garner customer loyalty. By taking these measures, businesses can reduce risks and ensure that their products are of the best possible quality.
What are the 3 types of quality control?
Usually, quality inspections are conducted during the pre-production stage of a product's development in order to detect any potential problems with the product. In-line inspections look at the product itself, from the inside out. Final inspections are conducted once the final version of a product is complete and ready for release.
What is quality control in simple words?
Quality control (QC) is a procedure or set of procedures intended to ensure that a manufactured product or performed service meets the requirements of the client or customer. QC is similar to, but not identical with, quality assurance (QA). QC is important for products and services because it can help ensure that the product or service meets customer requirements and expectations. QC can also help ensure that the product or service is reliable.
How do you answer interview question about quality control?
In quality control, there are many different ways to test products. Some common types of testing include unit testing, functional testing, and integration testing. By using these tests, you can ensure that the products you produce are of the highest quality possible.
What are 5 different quality control methods?
Quality control is an important process that is needed to ensure the quality of a product. There are seven primary quality control tools which include checklists, Fishbone diagrams, control charts, stratification, pareto chart, and histogram. The purpose of these tools is to help identify problems and make improvements.
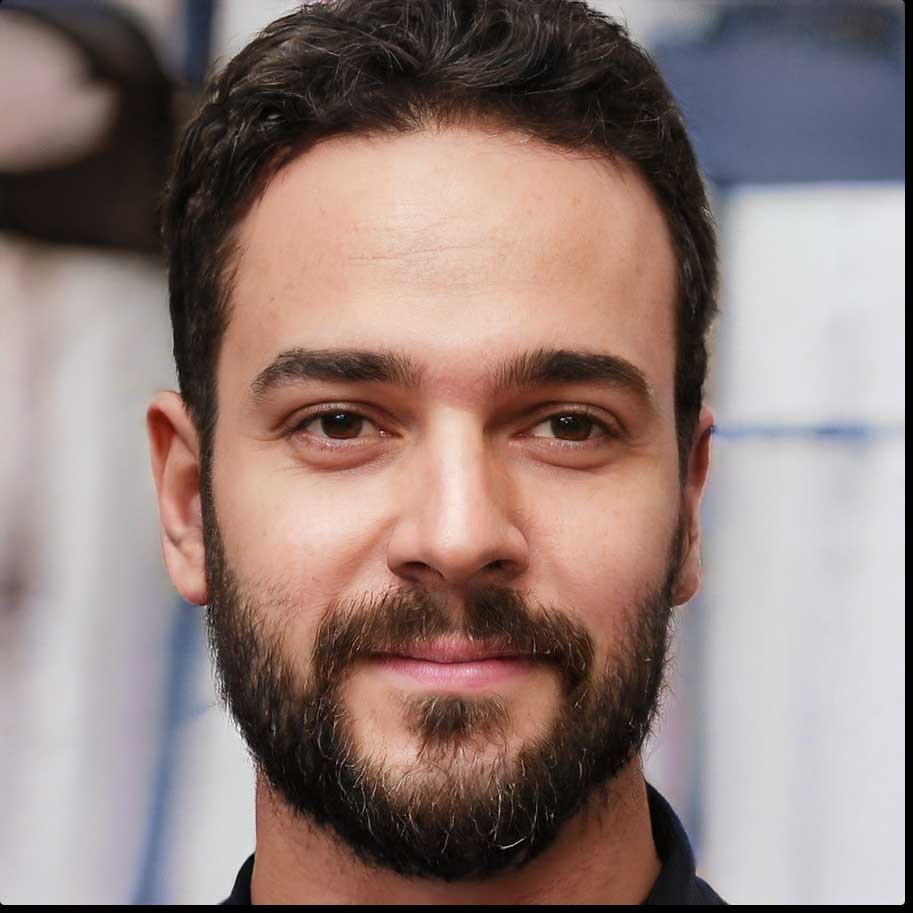