QUALITY CONTROL ADMINISTRATOR JOB DESCRIPTION
Find detail information about quality control administrator job description, duty and skills required for quality control administrator position.
What is the role of a quality administrator?
It is important for the quality administrator to constantly assess the quality of company products using analytical information. This allows them to make sure that products are of high quality and meet customer demands. They would also provide assistance to the quality department and making sure documentation is updated correctly.
What are the skills required for quality control?
When it comes to testing, QA is a must. By taking the time to understand and apply the specific testing requirements of a product or service, QA can ensure that your product or service is of high quality and meets customer needs. In order to be successful in QA, you?ll need to be attentive to detail, have good time management skills, and be able to solve problems quickly. As a part of a team, you?ll also need to be knowledgeable about quality standards. By creating high-quality and user-friendly products or services, you can ensure that your customers will love them and recommend you to others.
What is the job of a quality control employee?
A quality control inspector is responsible for monitoring the quality of incoming and outgoing products for manufacturing companies. Quality control inspectors, also called quality controllers (QC), are members of a control audit team that examine manufacturing processes and operational techniques. They are responsible for ensuring that products meet specific standards set by the company.
What are the duties of quality control manager?
A quality control manager oversees the quality of products and helps ensure they meet customer requirements. This person is responsible for ensuring products are of excellent quality and are able to meet efficiency and quality standards. They work with clients to ensure that final products meet their needs and requirements.
Is quality control a good career?
Quality control and assurance professionals work in a variety of industries, from aerospace and automobiles to pharmaceuticals and food. They need a keen eye for detail, strong communication, planning and problem-solving skills.
What qualification do you need to be a quality manager?
A quality manager, also known as an entry-level position in the business world, is responsible for leading and controlling the quality of products and services. This position typically requires a degree in a related field such as business or quality control. Many students choose to pursue a career in this field after completing undergraduate coursework in mathematics, systems management, measurements and business management.
What is quality control experience?
QC is the practice of ensuring consistent quality throughout a manufacturing process and also uniformity in a company's products. A large number of scientific and technical companies will have dedicated QC departments however QC is also required in a range of other industries. A key part of QC is ensuring that products are made to specification, which can be difficult in some circumstances. However, with the right techniques, it can be done.
How do I write a quality control resume?
"I am a quality control specialist with experience in various aspects of the production process. I have a strong understanding of the importance of quality and how to ensure it is maintained in all areas of my work. I am confident that I can play an important role in helping your company maintain its high standards." - source.
What are the 4 types of quality control?
The four types of quality control are an x-bar chart, Six Sigma, 100% inspection mode, and the Taguchi Method. The x-bar chart is a simple way to measure the quality of a product. It consists of a series of bars that represent the level of quality for each category. The higher the bar, the better the product. The Six Sigma method is a way to measure how well a company is performing in terms of quality. It uses guidelines to help employees achieve high levels of performance. The 100% inspection mode allows for complete accuracy and reliability in all phases of production. This ensures that all products are meeting the same high standards.
What is the salary of quality control officer?
The Control Officer salary in India ranges between ? 1.7 Lakhs to ? 5.2 Lakhs with an average annual salary of ? 3.1 Lakhs. The Control Officer job is a responsible position and requires a lot of dedication and hard work. The Control Officer salary in India also depends on the geographical location, experience, and other qualifications of the applicant.
What are some examples of quality control?
QC ensures that the product being developed is of the required quality. Inspection, deliveryable peer reviews and software testing help to ensure that the product is ready for use.
What are the 5 roles of a quality supervisor?
A supervisor is responsible for ensuring that all production lines or departments are meeting company standards. They also need to be attentive to employee attendance and take disciplinary action if necessary. In addition, the supervisor is responsible for managing projects involving a team of employees working on specific tasks towards common goals.
Is quality control a stressful job?
It can be a bit exhausting work, but it's definitely not as challenging as many other office jobs. QA specialists are responsible for verifying product requirements and performing risk assessments. They also need to improve the quality of the product in order to make it more marketable. Additionally, they may need to test the product in order to ensure that it meets all of the company's expectations.
What is next after quality control?
A Quality Control can determine their career goals through the career progression. For example, they could start out with a role such as Quality Assurance, progress to a title such as Quality Assurance Lead and then eventually end up with the title Quality Assurance Manager. A quality control's job is to ensure that products and services are of the highest quality possible. By being able to identify and correct potential problems early on, quality control can help avoid costly customer service issues.
What are the 5 types of quality control?
In order to ensure quality in your product, you should maintain a checklist of key items and use control charts, stratification, and pareto charts to better understand how each individual part of the product is performing.
What are the 3 main objectives of quality control?
In a quality control system, the three main objectives are to enhance product quality, reduce risks, and garner customer loyalty. By doing so, the company can achieve production efficiencies and avoid costly mistakes.
What skills can you put on your resume?
Since he was a child, Joe has loved writing. He has always found the process of composing and putting together a piece of writing to be pleasurable, and he enjoys working on his own work as much as collaborating with others. Joe has excellent writing skills and is able to communicate effectively with others. He is also adept at problem-solving, which comes in handy when it comes to his work at the company.
What is a quality inspector position?
A quality inspector is a professional who inspects products for compliance with company standards. They use tools and company guidelines to make sure products meet all requirements.
What are the 2 types of quality control?
Inspection is a common method used for quality control purposes not only in production but also in services. Statistics show that inspection can help to improve the quality of a product.
What are the 3 types of quality control?
When a company is looking to produce a new product, they will likely use a variety of inspections in order to detect any potential quality problems. These inspections can include pre-production, in-line, and final. Pre-production inspections are important in order to ensure that the product is of the correct quality. They will look at things like the design and material used in the product. This will help to ensure that any manufacturing defects are detected early and corrected. In-line inspections are used when a product is being produced right on site. This means that there is no need for shipment or transport to be made beforehand. This allows for faster production and better quality control. Final inspections are used when a product is ready for market. They look at everything from the packaging to the finished product itself. This will help to ensure that all aspects of the product are of good quality and meet customer expectations.
What are the 3 types of quality?
In any industry, basic quality is the most important factor to consider when creating a product or service. This assures that the customer's satisfaction is absolute and that the company can continue to make profits. In addition, performance quality should be considered when choosing a supplier, as it affects customer satisfaction as well. Excitement quality is critical for businesses in any industry, as it helps create an atmosphere of excitement and anticipation around their products or services.
How do I become a quality control engineer?
QA engineers are responsible for ensuring that products and services offered by companies are of high quality. They work with developers to develop products that meet customer expectations, and they use various quality assurance tools to ensure that these products are safe and effective.
What is the full form of QC?
QC is a procedure or set of procedures intended to ensure that a manufactured product or performed service adheres to a defined set of quality criteria or meets the requirements of the client or customer. QC can be used to ensure the quality of products and services, as well as to ensure that they meet specific customer requirements.
How do you answer interview question about quality control?
Quality control testing is a critical part of any organization's quality management system. It ensures that products and services meet the expectations of customers and employees. Testing can be conducted in a variety of ways, including unit testing, functional testing, and integration testing.
What is the main objective of quality control?
Quality control is a process that ensures the product meets the standards set by the company. This process includes measuring and testing every product, samples from each batch, or random samples to make sure the business is meeting its own standards. The main objective of quality control is to ensure that the business is achieving the standards it sets for itself.
How do I become a quality control supervisor?
A quality control manager is responsible for ensuring that products meet the required standards and that crew members are able to complete their jobs safely. They must be able to communicate effectively with both management and production line staff, as well as create reports that help to improve safety.
How do you become a quality control supervisor?
A quality control supervisor is responsible for ensuring the quality of products and services delivered to customers. They work with other parts of the company to monitor and measure the quality of products and services. A quality control supervisor can also be found working with suppliers to ensure that products are meeting specific standards.
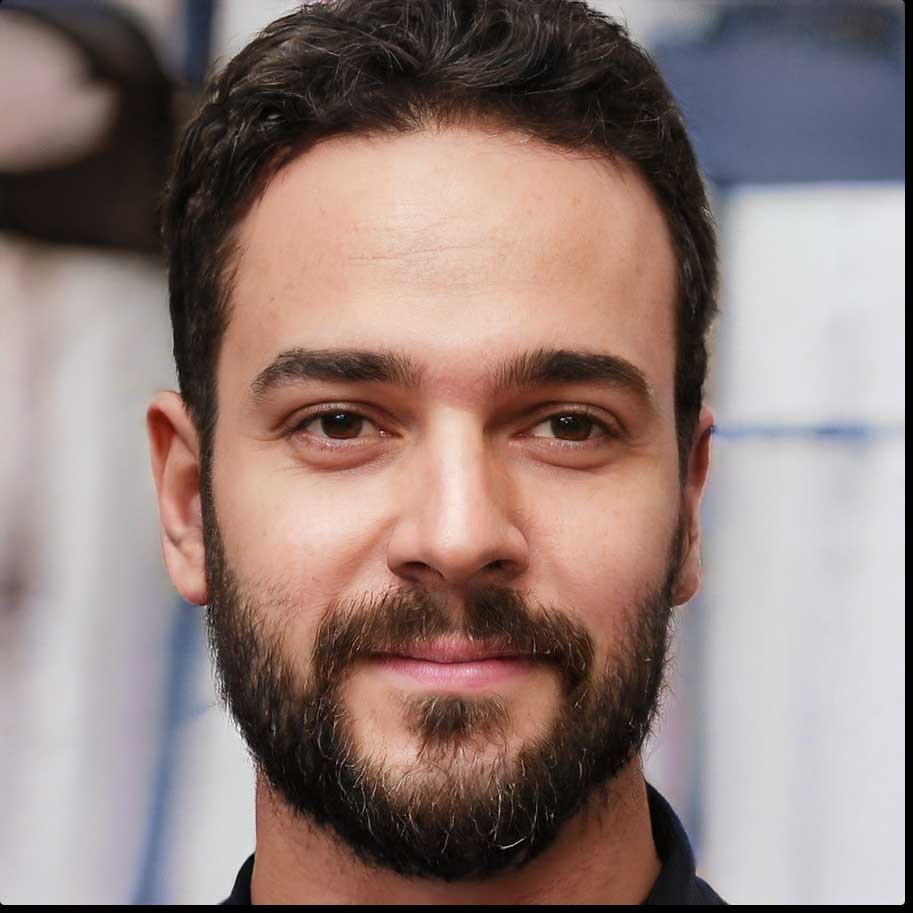