PLANT QUALITY MANAGER JOB DESCRIPTION
Find detail information about plant quality manager job description, duty and skills required for plant quality manager position.
What should quality manager do?
Quality management is a critical function within any organization. It ensures the products and services that are offered to its customers meet quality standards and meet customer expectations. Quality control processes include identification of quality problems, determination of the severity of the problem, and corrective action.
What is a plant managers job?
In the morning, the plant manager is at the helm of the plant. They are responsible for all of the daily operations as well as long-range plans. The plant manager is always working to make sure that their factory produces products that meet customer's needs.
What qualifications do you need for quality manager?
In order to be a successful quality assurance or quality control specialist, candidates must have a Bachelor's degree in business or a related field, five or more years of experience in a quality assurance or quality control position, and strong organizational and leadership skills. Additionally, ASQ quality control certification is preferred. As a result of these skills, an ASQ quality control specialist can help improve the efficiency and effectiveness of organizations by providing valuable insights into the quality of products and services.
What are the skills of a quality manager?
A quality manager is responsible for ensuring the quality of products and services, by ensuring that the products and services are meet customer requirements and that no client interaction is wasted. They work with their team to ensure that all tasks are completed in a timely manner, and that all projects are successful. A quality manager oversees an organization?s physical, emotional, and cognitive infrastructure so that they can provide the best possible service to their customers. They work with their team to ensure that all tasks are completed in a timely manner, and that all projects are successful. They also have a strategic view of how the organization should be run, which allows them to make informed decisions about where resources should be spent.
What are five 5 typical roles and responsibilities of quality management personnel?
A quality manager is responsible for ensuring the accuracy, consistency, and quality of products. They collect data to help identify any potential problems and work to improve processes in order to ensure a high level of product quality.
Who reports to quality manager?
The quality manager is a real manager who reports at the same level as the managers he or she measures and reports about. This makes it easy for him or her to understand what is happening and make needed changes.
How do I become a plant manager?
Plant managers must have a Bachelor's degree in business administration or industrial engineering, or a degree closely related. However, if plant workers have several years of experience, they have the opportunity to take management classes so they can be promoted to plant manager. Plant managers are responsible for managing and maintaining a plant, which may include directorship of a plant department, leadership of a team of workers, or management of resources used in the plant.
How can I be a good plant manager?
If you're looking for a plant manager who is able to lead and make decisions, you'll want to look for someone with leadership skills. They should be able to communicate effectively, be positive and adherent to quality standards, be efficient with their time and have the ability to learn.
How do you interview a plant manager?
A Plant Manager's daily priorities may vary, but they typically include ensuring that their plants are of high quality,etermining the best ways to save money and improving plant efficiency. They may also set long-term objectives and assess progress on these goals.
Is quality control a good career?
Quality control and assurance is a field of science that deals with the prevention and detection of quality problems in products. Quality control officers are responsible for ensuring that products meet the required specifications. They also work to maintain the quality of their own productions by observing and monitoring their own factories. Quality assurance officers often work in teams, and typically have a strong communication skills. They are also able to plan and manage projects, which can be difficult tasks when it comes to ensuring that products meet specific standards. In many cases, quality control officers may also be involved in the development of new product technologies.
What is the most important attribute of a Quality Manager?
Most people would agree that leadership is one of the most important skills a team can possess. Leaders are able to inspire others to achieve great things, and are often in a better position to know what needs to be done in order for their team to succeed.
What does a QA QC manager do?
A quality assurance, or quality control, manager is typically responsible for ensuring all relevant quality standards for whatever product a business produces. The manager must ensure that products are of the highest quality possible and that customer satisfaction is always a top priority.
What is the first step of Qa?
QA is the process of verifying the accuracy of a product before it is released to the public. Quality assurance (QA) includes identifying customer need, understanding how the product will be used, and measuring results to ensure that quality is maintained. In order to ensure customer satisfaction, QA involves collecting information from users, understanding their needs, and conducting tests.
What are the 4 stages of quality management?
In the early days of quality management, inspectors looked for errors in products. As quality improved, inspectors became more focused on detecting how products were performing overall and not just individual elements. In the third stage, quality control focused on verifying that each product was meeting requirements from the beginning to end. This involved checking for manufacturing defects, inspecting finished products for features that could cause defects, and testing products to ensure they met requirements. In the fourth stage, quality assurance focused on ensuring that all aspects of a product are correct before it is released to the public. This involved verifying that materials are used in accordance with specifications, checking for manufacturing errors, and testing products to ensure they met requirements.
What is quality quality management?
In order to maintain an excellent level of quality, management must determine a quality policy, create and implement a quality planning and assurance process, and test and measure the effectiveness of their measures. They also need to ensure that all employees are aware of the company'squality policy and what is required for success.
What should I ask a quality manager?
"I am a quality management consultant and have worked in the manufacturing and service industries. I can say that the most important attribute of a quality manager is to be able to delegate tasks effectively. It is also important to have good communication skills, as it is often difficult to manage tasks if one person cannot understand them. Another important attribute of a quality manager is to be able to work with other departments in order to achieve common goals. I have worked in companies where the quality assurance manager was responsible for all aspects of production and made sure that products were meeting customer expectations." - source.
Is it hard to become a plant manager?
A plant manager is responsible for leading and managing a plant, which includes the daily operations of the plant and its personnel. Plant managers must have excellent problem-solving skills and be able to manage various deadlines. A degree in business management or other related field is necessary to be a plant manager.
What level of management is plant managers?
Middle-level managers are responsible for carrying out the goals set by top management and working with their lower-level counterparts to achieve success. In many industries, middle managers have a broadened perspective that allows them to understand the entire organization and its constituent parts. They are also responsible for developing and implementing plans that allow the organization to reach its goals.
Who is above plant manager?
A general manager oversees all aspects of a company's operations, from the planning and execution of projects to the day-to-day running of the business. This position can be extremely demanding, but with a well- trained and experienced workforce, a general manager can lead a company to great success. A general manager needs to have strong leadership skills and be able to motivate his or her team members. Many companies today place a high importance on innovation and technology, which demands an understanding of business concepts as well as technical expertise.
How many hours do plant managers work?
A plant manager typically works 40 hours a week. This can include shift work to cover leave and sickness. A plant manager often works over these hours to make sure paperwork and other administrative tasks are completed satisfactorily.
What should a manager do in the first 90 days?
In the first 90 days, take the time to learn more about your team and their work. Create a plan and set clear expectations for yourself. Be willing to listen to employees and get feedback. You'll be able to improve your team's work performance in no time!
Why is plant maintenance important?
In agriculture, plant maintenance plays a prominent role in production management because plant breakdown creates problems such as loss in production time, increase in spoilt materials form sudden stoppage of process damages in-process materials, failure to recover overheads (because of loss in production hours) and the need for costly repairs.
What should I ask a plant manager?
The Plant Manager is responsible for the overall daily operations of a plant. They are in charge of ensuring that the plant produces the desired results. The Plant Manager should be able to work with their team to set long-term objectives and evaluate them regularly. They should also have a strong understanding of quality assurance, which can include setting standards and issuing directives to employees.
How badly do you need this job answer?
"I am interested in the position and would love to apply. I am a hard worker who takes pride in my work. I have experience working with computers and enjoy working on tasks that are challenging." - source.
How do you answer tell me about a challenge you had to overcome?
"I faced a challenge when I was hired as a new employee at my company. The company was struggling and I wanted to help. I researched the company and found that it was in need of a new marketing director. After much debate, I decided to apply for the position. The challenge was to come up with an effective marketing strategy for the company. My team and I worked hard to create a plan that succeeded. They were able to achieve the goals and improve the company's image." - source.
Is quality control a stressful job?
When it comes to quality assurance, anyone can do a good job. A QA specialist, on the other hand, has a lot of experience and knowledge to bring to the table. The work is not as demanding as it may seem at first glance, and there doesn't seem to be much burnout involved. In fact, this type of job can lead to some really great skills that you can use in your career.
What is the salary of quality control officer?
The salary of a control officer in India varies from ? 1.7 lakhs to ? 5.2 lakhs with an average annual salary of ? 3.1 lakhs. The control officer job is a key role in any company and brings with it many duties and responsibilities that can lead to an annual salary of more than Rs. 5 lakhs. This is an excellent opportunity for someone with the right skills, determination and experience to start their own business or take up a career in corporate management.
What is the 3 qualities of manager?
13 soft skills that make managers great are communication, comprehension, appreciation, consistency, and reliability. They must be able to have a strong connection with their team and be able to make sound decisions.
Which is better QC or QA?
QA is the process of ensuring quality in products or services. By definition, QC is the checks and balances that are put in place to ensure that products or services are of a high quality. QC measurement results can be used to correct/modify QA processes which can be successfully implemented in new projects as well.
What are the 4 types of quality assurance?
Pre-production inspection (PPI) is the process of verifying that the product being produced meets all the necessary quality requirements before it is released to consumers. PPI also includes checking to see if any defects have been found during manufacturing and ensuring that products meet customer expectations before they are put into production. Production inspection (DPI) is the process of checking products before they are released to consumers and includes inspecting each piece of product to make sure it is fitting properly and meeting all necessary safety requirements. DPI also includes verifying that products are being manufactured in a consistent manner, ensuring that there are no unauthorized changes or modifications to the product. Pre-shipment inspection (PSI) is the process of verifying that products will be shipped on time and meet all necessary safety requirements. PSI also includes checking for any problems with product delivery, ensuring that products are delivered in a safe and timely manner.
What is quality assurance PDF?
QA is a critical step in the manufacturing process that ensures that a product meets quality and performance requirements. QA takes many different forms, but all aim to ensure that products are fit for use. Some common QA activities include reviewing product features, checking tolerances, and verifying the quality of materials used in a product.
What is quality testing?
Quality control is a process through which you achieve, or improve, product quality. It is important to set up a quality control mechanism in order to ensure that your products meet the expectations of your customers.
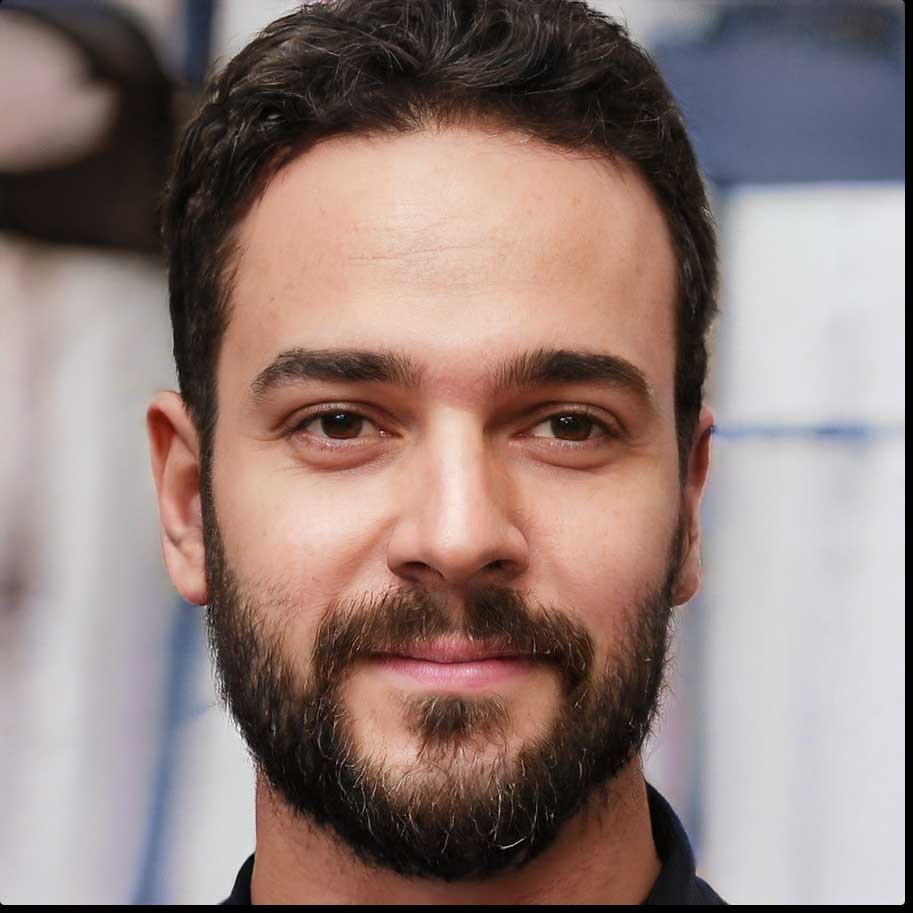