MATERIAL CONTROL COORDINATOR JOB DESCRIPTION
Find detail information about material control coordinator job description, duty and skills required for material control coordinator position.
What does a material control coordinator do?
The coordinator responsible for inventory management is responsible for a broad range of duties related to the oversight of products and materials. They inspect and record shipments, and may also handle the processing of maintenance requests and work orders. In their role, the coordinator is a key player in ensuring that products are delivered on time, as well as maintaining an accurate inventory.
What does a material control clerk do?
A production supervisor oversees the entire production process, from the planning stages through to the final product. They work closely with department supervisors to ensure thatProduction goals are met and that shipments are completed on time. They also compile reports on progress of work and inventory levels, costs, and production problems.
What is a material administrator?
As a project manager, your job is to ensure that all tasks are completed on time, within budget, and to maintain communication with other team members. You must be able to create and manage project files and track progress through reports. You also need to be able to communicate effectively with clients and other team members.
What is procurement coordinator?
The procurement coordinator oversees the purchase of materials for an organization. They are responsible for ensuring that all necessary supplies are purchased and used in an effective way. They work closely with the CEO to ensure that all goals and objectives are met, and that the organization is able to operate efficiently.
What is material coordination?
A material coordinator is responsible for managing the flow of materials and supplies. This position is commonly found in the construction, distribution and manufacturing sectors. The accurate and timely management of shipments is central to the cost-effective operation of businesses in these industries. A material coordinator must be able to handle sensitive material shipments with accuracy and regularity to ensure the success of their business. This position often requires excellent communication skills, as well as a strong understanding of business principles.
What is the role of a material planner?
Usually, the material planner's responsibilities include determining material specifications, creating and maintaining inventory schedules, coordinating with internal departments, and managing external stakeholder relations. The material planner is responsible for providing accurate information to departments in order to ensure timely shipment of needed supplies. Additionally, the material planner must be able to keep track of inventory levels and make necessary adjustments in order to ensure that necessary supplies are always available.
What do you understand by material control?
A material control system helps ensure that materials are flowing in a regular and uninterrupted manner in the production pipeline. By controlling the storage, purchase, and usage of materials, this system can help keep the production line running smoothly.
Is inventory control a skill?
An Inventory Controller needs strong writing skills in order to effectively manage inventory and make informed decisions. They need to be able to communicate effectively with customers and other team members, as well as keep track of information. Additionally, they need to be able to use their knowledge of inventory systems in order to forecast future demand and planinventory accordingly.
What is inventory job description?
The Inventory Clerk, or Inventory Associate, is responsible for organizing and controlling the stock of goods and supplies in a store or warehouse. Their duties include signing off on shipments, counting the number of available products and placing orders for more inventory according to demand. They are an essential part of any business, and their work can help support sales or production.
What are the skills required in a material manager?
The company has a strong supply chain and inventory management system that allows for efficient and accurate forecasting and budgeting. The organization and time-management skills of the employees are also very well suited for running the company. The communication and leadership skills of the employees are also very important in managing a company.
What are the qualities required for material manager?
A materials manager is responsible for managing and organizing all the materials used by a business. They must be familiar with supply chain and inventory management systems, as well as forecasting and budgeting. Additionally, they must be excellent at working with MS Office, as well as being able to manage difficult projects.
How do you become a Materials Manager?
In today's economy, material managers play a critical role in every organization. They are responsible for organizing and controlling the physical resources used in an organization, from buying materials to storing and distributing them. Material managers must be able to thinkoutside the box to come up with new ideas for how to improve the efficiency of an organization's operations. They also need to be able to work with other departments in order to make sure that all aspects of an organization are taken into account when planning materials needs. A bachelor's degree in business or a related field is essential for any material manager. Experience as a manager or supervisory position is also helpful.
What are the 4 main roles of procurement?
At a company, everyone is responsible for the success of the organization. From procurement to marketing, everyone has a role in achieving the organization's goals. The Procurement Process is an important part of this process, and it is important to have strong relationships with other functional groups. One way to have these relationships is by developing strong procurement policies and procedures. Another way to achieve objectives is by working closely with marketing to promote the company's products.
What is a procurement specialist do?
A procurement specialist is responsible for a myriad of processes including supply chain management, evaluating suppliers, purchase orders, purchasing goods or services, and contract negotiation. They work with clients to identify the best options for meeting customer needs and ensuring quality. The procurement specialist is also responsible for developing and implementing supply chain plans and strategies.
What does a procurement facilitator do?
Usually one of the purchasing managers coordinates the procurement functions, supplier relationships and stock management processes within their department. This allows them to ensure that high customer service levels and best value are achieved for the organisation.
Who is logistics coordinator?
The logistics coordinator is responsible for ensuring a smooth process and effective distribution of products. She is responsible for coordinating the movement of goods within the company, as well as ensuring that products are delivered to their destination in a timely manner. The logistics coordinator also has a responsibility for monitoring the quality of goods in the company's supply chain, and ensuring that products are received in good condition.
Is material planner part of supply chain?
A materials planner helps a company keep its inventory high and produce the products it needs, but also doesn't have to worry about large amounts of material that could be lost or stolen. They have a degree in logistics, supply chain management, or a related subject.
What is material scheduler?
Usually, the job of a materials scheduler falls into two categories: those that keep track of what is being produced and those that help with the distribution. The materials scheduler in the production line will be responsible for keeping track of all products, ensuring they are delivered on time and to their destination. They will also be responsible for helping to distribute products to meet the necessary needs.
What is material planning and budgeting?
One of the most important aspects of budgeting is to be able to identify what materials will be used in a project and at what price. This information can be used to generate a material budget that accurately reflects the purchasing power of the funds.
Why material control is important?
Raw materials are a valuable and important part of any business. To avoid overstocking and understocking, it is essential to have enough of them. This helps to ensure proper storage and safety of materials.
What are the two levels of material control?
When it comes to controlling the amount of material that someone manufactures, quantity control is key. This means making sure that the amount of items that someone produces is consistent and not too much or too little. Financial control is also important when it comes to manufacturing. This means ensuring that someone has enough money to buy what they need and not too much or too little.
What are the disadvantages of material control?
Material planning is important for any business. It can help to align the company's actual figures with what is needed to achieve a desired outcome. Implementation of material control policies can be harder because of a number of factors beyond the company's control.
What are the 4 types of inventory?
Inventory is the process of tallying up all the items in a store. It can be used to track sales, inventory levels, and more. Raw materials and components are the most important type of inventory, as they are necessary for making products. WIP is also important, as it shows how many products are currently in stock and how much work needs to be done to improve the product. Finished goods can also be important, as customers may want to buy a certain product but not yet have it in stock.
How do you describe inventory control on a resume?
Inventory Control Clerk, as a position title, may conduct inventory control tasks such as receiving and counting stock items, and recording data manually or using a computer. As an inventory control clerk, you will need to be able to identify discrepancies or adjust errors. In this position, you will work in a team environment and must be able to think critically.
How do you describe inventory management on a resume?
The warehouse employee oversees the tracking of deliveries, shipments and stock levels in the company's inventory. This individual evaluates shipments and product levels to improve the inventory control procedures. The warehouse employee is also responsible for managing the inventory tracking system. This system records deliveries, shipments and stock levels in a manner that allows for efficient inventory management.
Who is responsible for inventory?
Inventory managers are responsible for the stocking and management of inventory in a warehouse or similar facility. They lead a team of workers to receive and record new stock as it comes in and move stock onto trucks or shelves as needed. Inventory managers are responsible for ensuring that all products are quality controlled before they are put into circulation.
What are skills needed by an inventory clerk?
An effective inventory clerk needs excellent math and analytical skills as well as written and verbal communication skills. They should also be physically fit, have warehouse experience, and be knowledgeable of word processing, database and spreadsheet software.
Who reports to the Materials Manager?
Materials Manager is responsible for planning and forecasting customer orders to meet shipments. They work with product line coordinators on the planning and forecasting of customer orders in order to ensure that shipments are made on time and within budget. Materials Manager typically reports to a Head of a Unit/Department.
Who is responsible for material management?
When purchasing raw materials and finished goods, buyers are responsible for ensuring that the quality of products is up to par. To do this, buyers must compare prices and determine the quality of products a company will use to build products or sell to customers.
What is the difference between material management and supply chain management?
In today's business world, many businesses depend on the internet for their products and services. The internet has made it possible for companies to source materials from all over the world, and this has created a need for better management of the supply chain. One of the most important aspects of SCM is ensuring that all businesses in the supply chain are reliable and meet customer needs. This means ensuring that materials are properly stored, transported, and delivered to customers in a timely manner.
What is SAP MM module?
SAP MM (Materials Management) is a module in SAP ERP Central Component (ECC) that helps companies manage materials, inventory and warehouse operations. By providing customers with this module, companies can streamline their materials management processes and ensure they are able to avoid over-stock situations. Additionally, the module provides users with an easy way to track inventory levels, identify potential issues with material stock and more.
What is material executive?
The Overall Materials Management Executive is responsible for activities related to the purchase, storage, and distribution of raw materials, supplies, and equipment. They ensure that inventory needs are met throughout the production process while maximizing the efficiency of warehousing and distribution operations. This individual is also responsible for overseeing all manufacturing processes.
What is material handling experience?
Material Handler is responsible for monitoring in-process inventory and ensuring that all materials and supplies are delivered to production orders on time. They also keep the loading areas and machinery clean. This position is a great opportunity for someone with experience in the industry.
What are the 3 key functions in procurement?
When it comes to procurement, the company has a variety of options. One of the main procurement departments is responsible for centralizing the efficiency and compliance of these purchases. This department oversees direct and indirect procurements, as well as service procurements.
What are the 5 critical functions of procurement?
A procurement department is responsible for the management of procurements and the selection of the most appropriate suppliers for a given project. They also play a critical role in contracting and monitoring supplier performance. Procurement departments use various technologies to help them complete their tasks more efficiently.
What are the 3 types of purchasing?
A company might purchase a new product to replace an older one, or they might invest in a new plant to produce more efficiently. Mercantile purchasing refers to buying goods and services in order to gain an edge in the market. Industrial Purchasing refers to buying goods and services for the purpose of making them more efficient or producing more products. Institutions may also buy goods and services for the purpose of maintaining control over certain industries or regions.
What qualifications do I need to work in procurement?
A procurement professional must have a strong understanding of business and economics to effectively plan and execute procurements. They must also be able to communicate with various stakeholders involved in a project, including customers, suppliers, and the government.
Why did you choose procurement?
Procurement is a key sector that can offer a wide variety of different projects. Some may require a focus on analytics and delivering rapid cost savings, others may call for a more hands-on approach. With the world moving towards increasingly digital-driven economies, procuring goods and services in this way is essential to remain competitive.
Is procurement a good career?
A career in procurement can be very rewarding, as it can help companies save money and improve their operations. However, it is not just a one-way street: procurement also has a lot of potential for people who are already in the field. There are many opportunities to learn and grow in this field, and the right skillset can help you take your career to the next level.
How do I become a successful purchasing coordinator?
When it comes to purchasing managers, there are a few key things that they can keep in mind to help them excel. These include using innovative procurement tools and platforms, periodically reviewing vendors, developing strong relationships with your team and empowering your top performers to keep them engaged. Additionally, it's important for purchasing managers to write creative English paragraphs that communicate their ideas and experiences in a clear and concise way.
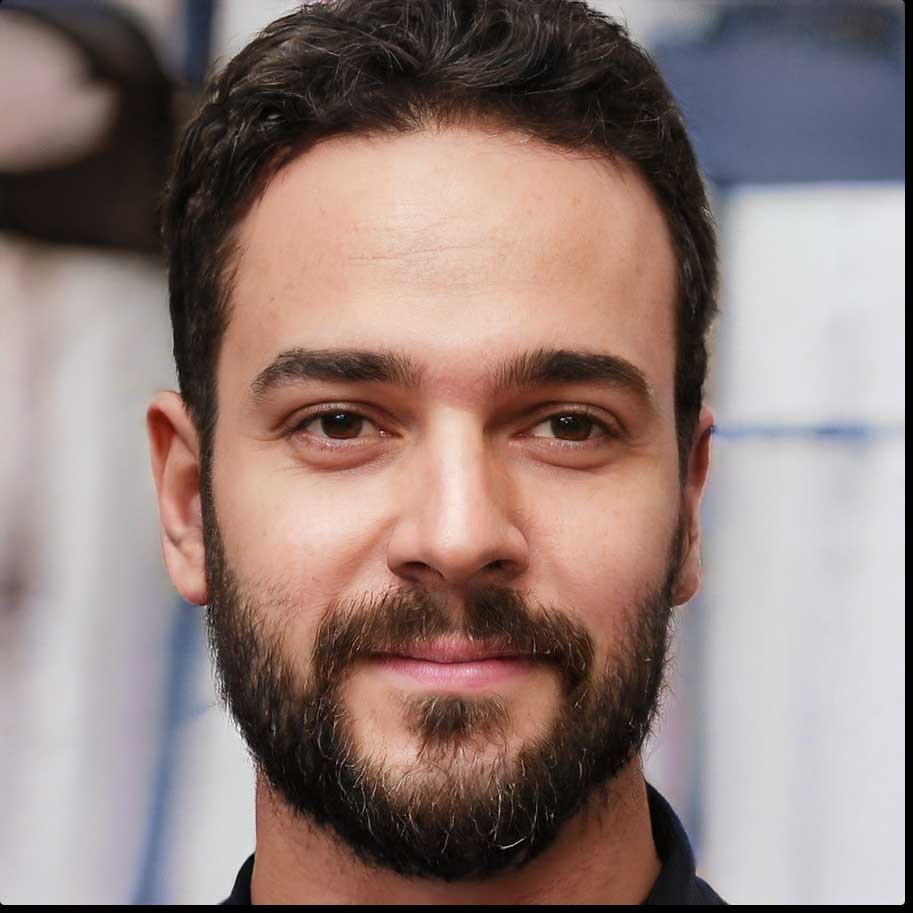