DIRECTOR OF MATERIALS JOB DESCRIPTION
Find detail information about director of materials job description, duty and skills required for director of materials position.
What are the skills required in a material manager?
The Nordstrom's brick-and-mortar locations are known for their high-quality and affordable clothing. The company also operates an online store, which sells clothes, accessories, and home goods. The Nordstrom's supply chain includes purchasing and shipping operations as well as inventory management. Inventory at Nordstrom's brick-and-mortar stores is managed using a variety of systems, including the company's own forecasting and budgeting software, as well as external vendors. In addition to tracking sales and inventory levels, Nordstrom also uses various communication tools to ensure that employees are kept up to date on the company's latest sales goals. Leadership skills are essential at Nordstrom, and employees are typically given clear instructions on what to do in order to meet store objectives. In addition to being able to rapidly adapt to changes in the business world, Nordstrom employees have excellent communication skills which enable them to keep everyone informed about what is happening within the company.
What is material management role?
Material Management oversees the purchase and disposition of materials for an organization. They are responsible for ensuring that equipment and products are bought at the lowest possible cost, shipping and receiving, and budgeting. They also manage purchasing processes, ensuring that all decisions are made in an objective manner.
How do you become a Materials Manager?
A material manager is responsible for organizing and managing materials. They must have excellent organizational skills and a deep understanding of forecasting and budgeting to ensure that their company's resources are used efficiently.
Who reports to the Materials Manager?
Materials Manager is responsible for planning and forecasting customer orders on the company's product line. They work with coordinators on the fulfillment of these orders, as well as communicating with customers about order status. Overall, this position requires a bachelor's degree in materials management or a related field.
What is material management with example?
The manufacturing process of a car requires the purchase of raw materials such as wheels, engines, and windows. The organization needs to plan and organize these steps to make sure that the finished product is quality and meets customer expectations.
What is material management in simple words?
Materials management is the process of organizing and controlling all materials used in a construction project so that they are requested in advance, obtained at a reasonable cost, and are available when needed. This can include everything from the materials that go directly to the construction site to the materials that are brought in on site. By understanding how materials are managed, it can help to ensure that projects run smoothly and cost less.
What are the five major areas of materials management?
Strong leadership and effective materials management systems can help a business succeed in the long term. A properly managed system allows for proper storage, handling, and distribution of materials, which leads to improved productivity and reduced wastes. By focusing on these key areas, businesses can create a successful launch that is both efficient and environmentally friendly.
Why material management is important?
Material management is important for any business to ensure the steady flow of goods for production purposes to satisfy customer demand. It also ensures production schedules are met. Moreover, it can help save production costs while maintaining product quality.
What are the functions of material manager in construction Organisation?
The materials manager is responsible for ensuring all materials needed for the business are procureable and available on time. They also work to ensure that the necessary resources are always available to meet the business objectives.
What is material executive?
The Materials Management Executive is responsible for ensuring that all raw materials, supplies, and equipment are properly stored and distributed throughout the production process. They also have overall responsibility for ensuring that inventory needs are met throughout the entire process. This allows for increased efficiency in warehousing and distribution operations.
What is the difference between material management and supply chain management?
In order to keep your supply chain running smoothly, it's important to have a reliable and efficient material management system in place. This system include supplies, inventory, and transportation management. By keeping track of these elements, you can make sure your supply chain is functioning as efficiently as possible.
What is material handling experience?
A Material Handler helps keep production areas clean and==ly stocked by delivering or opening products for clients. They also keep loading areas and machinery clean.
What are types of material management?
Material Management is one of the most important steps in any business. Not only does it need to ensure that materials are purchased and used in a safe and effective manner, but it also needs to ensure that the flow of materials is controlled and quality checked.
What is the main aspect of material management?
Material management is an important part of any business. It covers all aspects of material costs, supply and utilization. The functional areas involved in material management usually include purchasing, production control, shipping, receiving and stores. Material management is a necessary part of any business. It ensures that all materials are used efficiently and carefully. This helps to save time and money on every project. In addition, material management also supports the overall efficiency of the company. By doing this, the company can achieve its goals successfully.
What is material management in procurement?
There are a few things that go into making a good product. The ingredients, the manufacturing process, and finally the packaging. All of these are important in creating a successful product. Planning and anticipating the materials needed for a production process will ensure that your product is made with the best possible quality.
What is another name for material management?
Asset management is the process of managing assets such as property, equipment, or vehicles. This can include everything from planning and implementing repairs to disposing of assets when they no longer need them. Asset management can be difficult, but with the right tools and techniques it can be a very profitable activity.
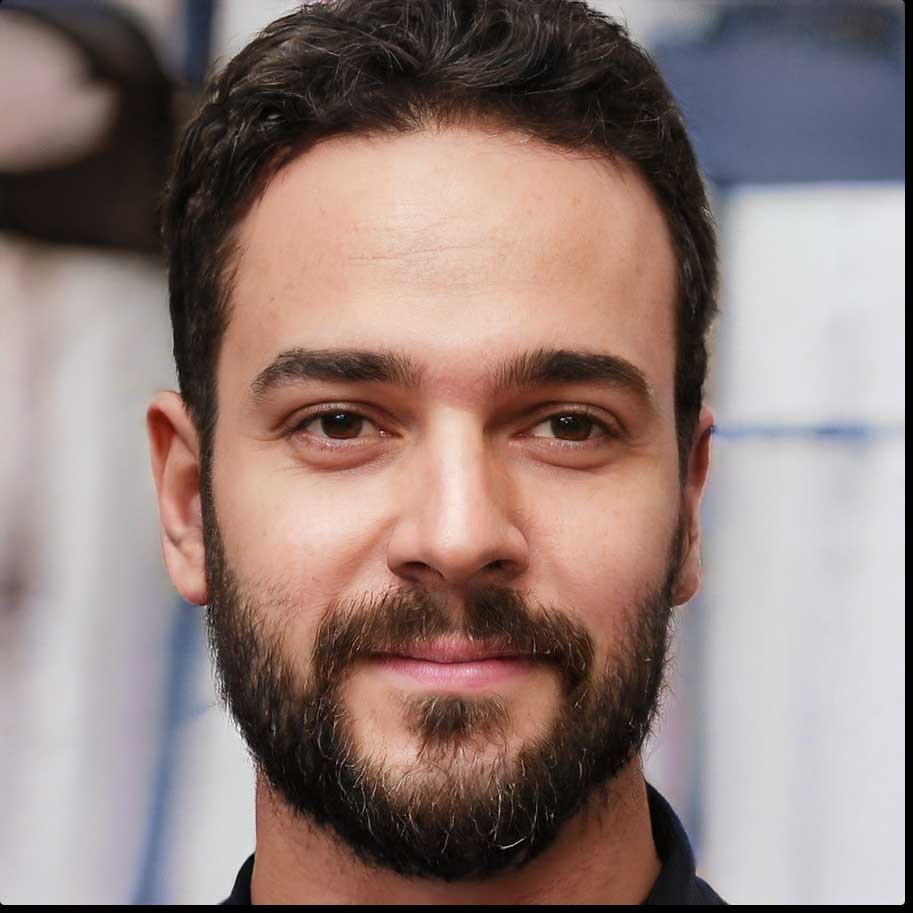